Hi Hans-Joachim: Thanks, it is precisely what I try to do after finishing any job on the Merkabah: paint, smile and go on.
The thing is that I realized that the original design included a central fin to reinforce the welding to deal with the long lever, and I had forgotten it completely trying to go on faster. Bad… and it was not the first time that I underestimated the forces involved. I want to do one and many Bremsprobes, of course, but convinced that the results will be remarkable.
And, by the way, if you know me a little by now, I am not the type of guy that worries about pointing fingers, he, he.
As soon as I arrived to the shop again I made a layout of the forgotten fins with cardboard and then chopped a little more the already skeletric frame of Spare and formed the fins using the power grinder. Once I was sure about the shapes and the measures I pinpricked the pieces in position. I decided to weld with the MIG at full power, just for the fun of it and to avoid welding again downside-up with 70/18 electrodes; it was not easy nor fun the last time.
Well, what’s the difference between the previous and the next picture? Let me tell you: two hours, many burnings on the fingers and the neck, repeated head strikes, low back pain, cramps and a dozen cursing and interruptions because the welding nozzle became obstructed continuously by molten electrodes - a gravity issue. I show you the worst support, the one with the less elegant welding cords, but that’s the way it came, proudly speaking, though.
I put in one of the old shock absorbers to calculate the right height for the superior support to maximize the range of movement of the axles with that given shock (stock). I marked the shock to make it centimeter by centimeter, to avoid mistaking; the idea was to profit of the range of the shock as much as possible and use it also to limit the vertical inferior movement of the axle, but it was already late and the game finished for that day.
The working place was full of dirt and metallic debris and before I started to work I powerblown and then swipped and cleaned the floor. When it was all a little more decent I took the hydraulic jack and lifted one and the other axle to make the bogie swing to examine the movement range, again, and also to check how the struts of the sway bar performed. All okay.
I marked the precise height for the support but there was a problem because there were only three supports at hand, two even, taller than necessary, and one with the right height, but alone; if you remember, I got them from the yellow Mercedes at the riverbed junk yard.
Almost started to fabricate a new pair of supports but I opted for the easier way and decided to modify the long supports; cut and drill… that was the solution. The simplicity and strength of the design could well manage the shortening.
There was another problem, though: the hole for the bushing bolt of one of the supports was torn, repaired and then torn again. I wanted to go the machineshop to use heavy tools for repairing it but in the end I decided not to complicate the issue more than necessary; I applied a little welding and then, patiently, grinded and powergrinded it until the result, far from professional, was at least acceptable.
After marking where the bolt holes went on the right side of the frame it was the turn to drill them. Oh, super-extra boring job! I really hate drilling the frame. After a while the holes were drilled and clean, and this time it came not so nasty because I put on the earphones with a selection of the very bests songs ever, at full volume. The music also blocked the radio station listened every day by the workers of the shop, with their unbearable regaeton and cumbias, at least unbearable to me.
Unfortunately the drill holes were closer than I wanted or recommended, but at least they would be near a couple of rivets, that are like two welding points between the rail frames. This time I allowed myself to say WTF!
I installed provisionally the support and the shock, make sure of all the measurements and put again the air spring to check if it all fitted and made sense, but it was late and I did not want to drill again not a single hole. I made some order and took Carmen back home on the Africa Twin, to eat something good.
Obviously, the next thing to do was to drill the bolt holes for the support of the left side of the frame, and so I did. Looking at them again they look not too bad, and the actual distance between them and the rivet holes is almost 4,5 mm.
But that was a strange day, and things were like that, strange; many difficulties to accomplish even little tasks and very few time to do it. It was time for priming the recently born/modified pieces but it was cold and someone said that it was probably going to rain.
I left the paint gun apart, took the broom and for the next hour I swept the hole place and made order, again. Every time I make some pressure to follow my own desired/imagined schedule things go wrong. Better take it easy now. Yes… I am learning.
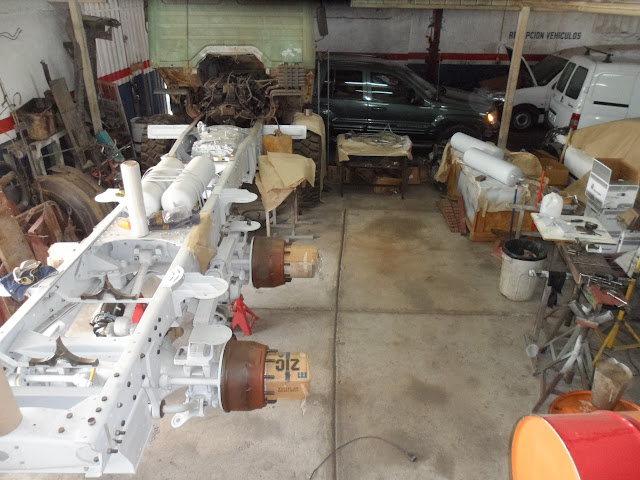